В современном производстве при получении художественных отливок, окончательная стоимость оказывается весьма завышенной[1,3]. Это вызвано тем, что при получении отливок художественного назначения приходится применять сложные литниково-питающие системы (ЛПС) и нестандартные схемы питания отливок, вследствие этого уменьшается технологический выход годного (ТВГ). Несмотря на это, большое количество отливок уходит в брак из-за поверхностных дефектов и вызвано это тем, что отливки художественного назначения, как правило, необходимо получать без дополнительной механической обработки.
Для снижения себестоимости готовых изделий, необходимо уменьшать количество металла расходуемого на ЛПС и элементы питающие тепловые узлы отливок (прибыли), также уменьшения количества необходимого расплава можно добиться получением полых отливок, для этих целей можно применить ряд методов получения отливок:
1. Применение установок литья противодавлением, вакуумным всасыванием и литья под низким давлением (Рис. 1), позволяющих получить отливку без ЛПС[2]. Принцип получения отливок данными методами состоит в том, что металл под действием разницы давлений по специальному металлопроводу входит в литейную форму и заполнят полость отливки. Основными преимуществами данных процессов литья являются: автоматизация трудоемкой операции заливки формы; возможность регулирования скорости потока расплава в полости формы изменением давления в камерах установок; улучшение питания отливки; снижение расхода металла на ЛПС. В данных установках также возможно получение отливок без прибылей, за счет того что питание отливки жидким расплавом происходит непосредственно в основной тепловой узел из металлопровода. Получение полых отливок данными методами затруднено тем, что при нормализации давления в камере с расплавом или формой жидкий метал под действием силы тяжести опускается обратно в тигель и в отливке образуется зона разреженности, что может привести к деформации полученного слоя твердой фазы на поверхности контакта отливки с формой. Данными методами все же возможно получение полых отливок, но необходимо производить расчет времени выдержки расплава для образования слоя твердой фазы на поверхности контакта отливки с формой необходимой прочности, способного противостоять усилиям деформации, возникающим вследствие действия зоны разреженности в массиве отливки.
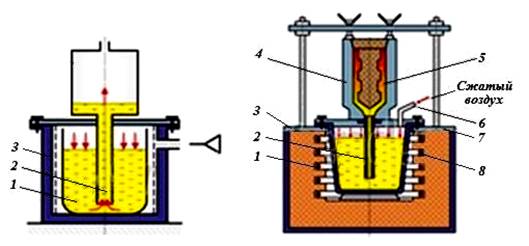
б
в
Рис. 1. Схемы и установки: а – литья под низким давлением; б – литья вакуумным всасыванием фасонных отливок; в – литья с противодавлением;
1 – тигель с расплавом металла; 2 – металлопровод; 3 – камера тигля;
4 – металлическая форма; 5 – отливка; 6 – воздухопровод;
7 – герметизирующая крышка; 8 – нагреватели; 9 – камера формы;
10 – подъемное устройство; 11 – вакуум-провод, соединенный с ресивером;
12 – разделительная плита; 13 – стержень; 14 – регулирующее устройство;
15 – манометр; 16 – отсекатель
Рис. 2. Схема получения стержней в полости формы:
1 – форма;
2 – удаляемый слой;
3 – стержень
2. Применение литья с внутренними стержнями (Рис. 2), позволяет получать отливки с заданной толщиной стенки, избегать возникновения усадочных раковин и утяжин на поверхности, за счет ликвидации тепловых узлов[4,5]. Но при данном методе необходимо учитывать влияние термического расширения стержней и усадки сплава, т.к. взаимное влияние этих факторов может привести к возникновению трещин, как на поверхности отливки, так и в основном массиве. Также при данном методе необходимо устанавливать прибыли для компенсации усадки сплава и необходимы ЛПС.
Чтобы избежать недостатков ранее описанных методов, можно применить метод литья «выливанием». Суть метода состоит в том, что после образования на поверхности контакта отливки с формой твердой фазы, производится поворот формы и жидкая фаза сливается. Таким образом, получатся отливка с заданным наружным контуром и полостью внутри. При данном методе нет необходимости в проектировании и конструировании ЛПС и прибылей, также нет необходимости в производстве стержней. Основной сложностью данного метода является то, что из-за сложной конфигурации художественных отливок, точный расчет времени выдержки расплава до образования твердой фазы на поверхности формы оказывается крайне трудоемким процессом и имеющим большие погрешности.
Для определения времени выдержки расплава нами был применен программный комплекс ProCAST. Комплекс базируется на методе конечных элементов, что обеспечивает высокую точность описания геометрии отливки и формы расчетной модели, учет большинства процессов теплового, кристаллизационного, металлургического, напряжено-деформированного характера. Для анализа была принята модель полусферы, за расплав принят эвтектический сплав на основе алюминия АК12, заливаемый в разовую песчано-глинистую форму (РПФ).
По результатам моделирования были получены данные представляющие зависимость толщины твердой фазы на поверхности контакта отливки с формой от времени выдержки расплава в форме. Данные представлены на (Рис. 3) и в табл. 1.
|
1
Step/Time Step: 585/1.000е+000 Total Time: 383.8275 sec |
2
Step/Time Step: 615/1.000е+000 Total Time: 413.8275 sec |
3
Step/Time Step: 645/1.000е+000 Total Time: 443.8275 sec |
4
Step/Time Step: 675/1.000е+000 Total Time: 473.8275 sec |
|
5
Step/Time Step: 705/1.000е+000 Total Time: 503.8275 sec |
6
Step/Time Step: 735/1.000е+000 Total Time: 533.8275 sec |
|
7
Step/Time Step: 765/1.000е+000 Total Time: 563.8275 sec |
|
Рис. 3. Результаты моделирования – этапы кристаллизации
Таблица 1
Зависимости толщины твердой фазы от времени выдержки расплава в форме
Время выдержки, с |
383 |
413 |
443 |
473 |
503 |
533 |
563 |
Толщина твердой фазы, мм |
1,28 |
2,32 |
4,12 |
4,63 |
5,15 |
6,7 |
7,73 |
После анализа результатов моделирования был проведен эксперимент при аналогичных условиях: марка сплава, материал формы и время выдержки. Результаты эксперимента приведены в табл. 2 и полученные образцы показаны на (Рис. 4.)
Таблица 2
Зависимости толщины твердой фазы от времени выдержки расплава в форме, полученные в ходе эксперимента
Время выдержки, с |
383 |
413 |
443 |
473 |
503 |
533 |
563 |
Толщина твердой фазы, мм |
1,5 |
2,73 |
4,40 |
4,84 |
5,75 |
6,95 |
8,30 |
а
б
Рис. 4. Толщина полученной твердой фазы на образцах:
а – при времени выдержки 563 сек. ; б – при времени выдержки 600 сек.
Полученные в ходе эксперимента результаты соответствуют результатам моделирования, из чего следует, что программный комплекс ProCAST возможно применять для оценки времени выдержки сплава на основе алюминия АК 12 в РПФ для получения необходимой толщины твердой фазы на поверхности контакта отливки с формой.
Рецензенты:
Сиротенко Л.Д., д.т.н., проф. каф. СПиТКМ МТФ ПНИПУ, г. Пермь;
Беленький В.Я., д.т.н., проф., каф. СПиТКМ ПНИПУ, г. Пермь.