Несмотря на то, что образование геля возможно напрямую из лиофобного золя, обычно применяют гелеобразующие агенты, в качестве которых могут быть использованы различные мономеры, образующие полимерные каркасы, или растворы полимеров [4]. С экологической точки зрения более перспективно использование водорастворимых полимеров как природного, так и искусственного происхождения. Так, в работе [8] использовали альгинат натрия, растворяющийся в холодной воде и обеспечивающий при добавлении фосфата кальция необратимое застудневание системы, в состав которой входит 50 (объемн.) % порошка глинозема. В работе [6] исследователи заключили, что использование в качестве гелеобразующей добавки производных агара является наиболее многообещающим в керамическом производстве.
Проведенные ранее в Научном центре порошкового материаловедения (НЦ ПМ) Пермского национального исследовательского политехнического университета исследования подтвердили перспективность использования природного полисахарида агар-агара в качестве гелеобразующего агента при получении пористых материалов на основе диоксидов циркония [7] и титана [9].
В работе [2] исследовано формирование структуры материала в процессе гелевого литья нанопорошка диоксида титана с применением в качестве гелеобразующего компонента агар-агара. В результате получен пористый диоксид титана (кажущаяся плотность 1,42 г/см3, общая пористость 65 %). Микроструктура материала исследована на изломе с помощью сканирующего электронного микроскопа ULTRA 55 (Carl Zeiss, Германия). На рис. 1 приведены полученные СЭМ-изображения. Пористый материал представляет собой трехмерный сетчатый каркас с толщиной образующих элементов 5–10 мкм. Поверхность излома материала отличается ярко выраженной слоистой структурой. Слои, в свою очередь, состоят из столбчатых элементов, диаметр которых соответствует размеру частиц исходного порошка, т.е. пористый материал оказывается результатом осуществления сложного процесса иерархического структурирования в условиях относительно свободного перемещения наночастиц.
При получении объемных керамических материалов и тонких пленок часто используется другое гелеобразующее вещество – поливиниловый спирт [3], являющийся синтетическим продуктом. Цель представленной работы – исследовать условия формирования пористых структур на основе диоксида титана с поливиниловым спиртом в качестве гелеобразующего агента.
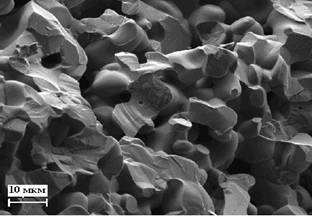
× 1000
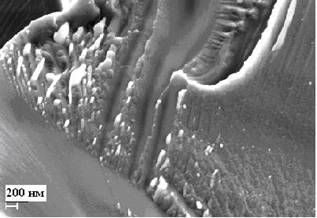
× 21000
Рис. 1. СЭМ-изображения изломов пористого диоксида титана при различных увеличениях
Материалы и методы исследования
В эксперименте использовали промышленный порошок диоксида титана марки «осч». Порошок представляет собой полидисперсную смесь частиц субмикронных размеров и использован в качестве более дешевой замены нанопорошка, синтезируемого в лабораторных условиях. Порошок предварительно прокаливали при температуре 900 0С для получения рутила. Однако в результате, по данным спектроскопии комбинационного рассеяния света, получена смесь рутила и анатаза, что является дополнительным подтверждением содержания значительного количества очень мелких фракций в составе порошка. Переход анатаза в рутил в микронных порошках фиксируется при 810–840 0С.
Образцы получали в соответствии с разработанной ранее технологической схемой (рис.2) [1]. Порошок активировали в 1 %-ном растворе поливинилового спирта (ПВС). В качестве гелеобразователя использовали 7 %-ный водный раствор ПВС. Соотношение порошка и жидкости во всех образцах было 1:1.
Использовали 3 варианта гелевого литья. В первом случае (контроль) шликер просто заливали в неактивную форму и высушивали на воздухе. Во втором и третьем экспериментах применяли лабораторную установку [1] с возможностью удаления излишков влаги вакуумированием с помощью водоструйного насоса. При этом во втором случае использовали, как описано в [1], фильтр из кордиеритовой керамики с бимодальным распределением пор. В третьем эксперименте фильтр не использовался. Высушенные заготовки спекали при 1350 0С в течение 1 ч.
Микрошлифы образцов изучали на оптическом микроскопе Axiovert 200M. Для подготовки микрошлифов образцы заливали эпоксидной смолой с вакуумированием.
Рис. 2. Схема получения методом гелевого литья пористых керамических образцов из наноразмерных порошков [1]
Фазовый состав образцов определяли методом спектроскопии комбинационного рассеяния света (КР-спектроскопии) на многофункциональном спектрометре комбинационного рассеяния света «SENTERRA» (Bruker) при длине волны излучающего лазера 532 нм.
Результаты исследования и их обсуждение
Все образцы в процессе сушки и спекания продемонстрировали значительную усадку и деформацию. Дефекты в основном образовались на этапе усадки, т.е. были связаны с потерей воды. Образцы сушили в оснастке, что привело к образованию трещин, связанных с прилипанием к стенкам формы (рис. 3). Наихудший вариант – контрольный образец. Наилучший – образец, сформованный с использованием слабого вакуумирования и кордиеритовой подложки в качестве фильтра. Вакуумирование без применения керамического фильтра привело к получению среднего результата. Таким образом, вне зависимости от того, какой гелеобразователь использовали при получении керамических заготовок, основные стадии процесса, предложенные ранее [1], остались неизменными. Определяющими в получении образцов гелевым литьем являются процессы образования и обезвоживания биконтинуальной структуры. От природы гелеобразователя зависит в основном вязкость суспензии.
а
б
Рис. 3. Образцы, полученные при различных вариантах осуществления процесса гелевого литья: а – заливка в неактивную форму, сушка в форме; б – заливка в неактивную форму, вакуумирование с применением керамической подложки, сушка в форме
Фазовый состав полученных образцов по данным КР-спектроскопии одинаков. После спекания в образцах присутствует только рутил (рис. 3).
Рис. 4. КР-спектр образца после спекания
Структуру образцов изучали с помощью оптического микроскопа. Снимки микрошлифов представлены на рис. 5. Во всех случаях получены пористые образцы. В процессе сушки геля на воздухе произошло существенное огрубление структуры с неконтролируемым образованием крупных пор. На рис. 5б представлен снимок микрошлифа образца, прошедшего при заливке стадию вакуумирования с применением пористой кордиеритовой подложки. Структура не только очевидно более мелкая, но и может быть отмечена ориентация пор, т.е. процесс частичного удаления жидкости вакуумированием препятствует огрублению структуры в процессе сушки и позволяет получить более мелкие поры у проницаемого керамического материала.
а б
Рис. 5. Структура спеченных образцов, полученных при различных вариантах осуществления процесса гелевого литья:
а – заливка в неактивную форму, сушка в форме;
б – заливка в неактивную форму, вакуумирование с применением керамической подложки, сушка в форме
Выводы
В эксперименте проверена возможность замены агар-агара на поливиниловый спирт в качестве гелеобразователя. Установлено, что
1. Вне зависимости от того, какой гелеобразователь использовали при получении керамических заготовок основные стадии процесса, предложенные ранее [1], остались неизменными. Определяющими в получении образцов гелевым литьем являются процессы образования и обезвоживания биконтинуальной структуры.
2. Структура образцов, полученных с применением вакуумирования, более мелкая, особенно при использовании кордиеритового фильтра-подложки.
Работа выполнена при поддержке Министерства образования и науки в рамках научно-исследовательского проекта № 1769 базовой части государственного задания Пермского национального исследовательского политехнического университета в сфере научной деятельности на 2014–2016 гг.
Рецензенты:Сиротенко Л.Д., д.т.н., профессор кафедры «Материалы, технологии и конструирование машин» ФГБОУ ВПО «Пермский национальный исследовательский политехнический университет», г. Пермь;
Оглезнева С.А., д.т.н., профессор кафедры «Материалы, технологии и конструирование машин» ФГБОУ ВПО «Пермский национальный исследовательский политехнический университет», г. Пермь.
Библиографическая ссылка
Мищинов Б.П., Порозова С.Е. ОПТИМИЗАЦИЯ УСЛОВИЙ ПОЛУЧЕНИЯ ПОРИСТОЙ КЕРАМИКИ ГЕЛЕВЫМ ЛИТЬЕМ СУБМИКРОННОГО ПОРОШКА ДИОКСИДА ТИТАНА // Современные проблемы науки и образования. 2015. № 2-2. ;URL: https://science-education.ru/ru/article/view?id=22981 (дата обращения: 18.08.2025).