Цементная промышленность является одним из крупнейших потребителей энергии, а именно топливных ресурсов, доля которых в себестоимости продукции составляет 30-40%. Особенностью цементной промышленности РФ является использование газообразного топлива при обжиге клинкера, поэтому многие научные исследования в настоящее время направлены на минимизацию топливных затрат путем замены части дорогого природного топлива более дешевым альтернативным.
Все большее внимание специалистов как перспективное технологическое топливо привлекает нефтяной кокс, являющийся отходом нефтеперерабатывающих предприятий, и по своим качественным характеристикам превосходящий многие природные топливные ресурсы.
Сырьем при получении нефтяного кокса являются тяжелые фракции нефти, образующиеся в результате атмосферной и вакуумной перегонки нефти (мазуты, полугудроны, гудроны), крекинг-остатки от термического крекинга мазутов и гудронов, тяжелые газойли каталитического крекинга, остатки масляного производства (асфальт пропановой деасфальтизации гудрона, экстракты фенольной очистки масел и др.). Из всех нефтяных остатков, склонных к образованию различных видов структур кокса, наиболее предпочтительными считаются ароматические концентраты (дистиллятный крекинг-остаток) и некоторые другие высокомолекулярные углеводороды.
Нефтяной кокс представляет собой твердый остаток вторичной переработки нефти или нефтепродуктов, получаемый при замедленном коксовании тяжелых нефтяных остатков. Основным назначением процесса замедленного коксования является максимальная выработка дистиллятов для последующего получения из них моторных топлив, а получаемый при этом нефтяной кокс рассматривается как побочный продукт, что и определяет его низкую стоимость.
В России эксплуатируется девять установок замедленного коксования различной мощности, и суммарный выход кокса в 2004 году составил 1089 тысяч тонн. Основными произвдителями кокса являются ОАО «Роснефть-Ангарская НХТ» (Ангарск, Иркутская область), ОАО «Роснефть-Комсомольский НПЗ» (Комсомольск-на-Амуре, Хабаровский край), ОАО «Роснефть-Новокуйбышевский НПЗ» (Новокуйбышевск, Самарская обл.), ООО «Лукойл-Волгограднефтепереработка» (Волгоград), ООО «Лукойл-Пермнефтеоргсинтез» (Пермь), ОАО «Газпромнефть-Омский НПЗ» (Омск), ОАО «НОВОЙЛ» (Уфа, Республика Башкортостан), ОАО «Уфанефтехим» (Уфа, Республика Башкортостан), ОАО «Завод”Cланцы”» (Сланцы, Ленинградская область).
Нефтяной кокс в отличие от натурального топлива имеет высокую удельную теплоту сгорания до 8000 ккал/кг, которая существенно превышает теплоту сгорания всех известных видов натурального твердого топлива. По ряду топливных характеристик нефтяной кокс является твердым аналогом мазута. Подобно мазутам нефтяной кокс отличается относительной дешевизной и низкой зольностью, которая колеблется в пределах 1%, что несопоставимо с зольностью ископаемых углей.
Нефтяной кокс может успешно применяться как в качестве части основного топлива, так и в качестве выгорающей добавки, вводимой в сырьевую смесь. Однако, если при использовании нефтяного кокса в качестве альтернативного топлива особых проблем не возникает, то при введении нефтяного кокса в сырьевую смесь либо шлам с целью экономии технологического топлива необходимо учитывать ряд параметров, причем применительно к используемому способу производства.
При рассмотрении возможности использования нефтяного кокса в качестве выгорающей добавки необходимо обеспечивать полное сгорание горючей составляющей, для чего необходима определенная температура и теплообмен в факельном пространстве при вынужденном значительном избытке воздуха. Кроме того, следует учитывать предельно возможную концентрацию выгорающей добавки в зависимости от технологических параметров работы вращающейся печи.
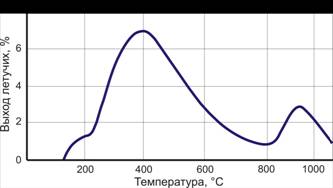
Рис. 1. Интенсивность выхода летучих из кокса в зависимости от температуры
На рис. 1 приведены результаты дифференциально-термического анализа кокса, которые свидетельствуют о том, что выход легколетучих практически начинается со 100-150ºС и наиболее интенсивно протекает в интервале температур 250–600ºС. Возможность воспламенения и выгорания легколетучей составляющей при 150ºС подтверждается исследованиями [5, 8].
При рассмотрении возможности полного выгорания летучих, выделяющихся в интервале 100-350ºС, следует отметить, что высокая скорость горения топлива обычно наступает выше 700ºС. Ниже этой температуры в промышленных топках, как правило, наблюдается недожог топлива [4].
В цементных агрегатах сухого способа, где теплообмен осуществляется в пылегазовой среде и, следовательно, температуры газа и материала практически совпадают, есть большая вероятность, что попавшие в низкотемпературную среду летучие топлива не успеют сгореть за несколько секунд в верхнем циклонном теплообменнике. В печах же мокрого способа производства совершенно другие условия – газовая фаза отделена от материала, и теплообмен происходит через поверхность слоя. При этом температура газового потока намного выше температуры материала.
Рис. 2. Экспериментально-расчетные значения температуры газового потока tг и материала tм по длине печи 4,5/5´170 м
Экспериментально-расчетные значения этих величин свидетельствуют, что температура газа в низкотемпературной области по крайней мере на 750ºС выше температуры материала (рис. 2), поэтому возгоняемые из материала летучие при 100-400ºС попадают в газовую среду с температурой 850-1150ºС, где произойдет их быстрое полное сгорание. Таким образом, температурные условия во вращающейся печи мокрого способа позволяют обеспечить выгорание горючей добавки материала даже, если выход летучих из материала происходит при 100ºС.
Следующим необходимым условием использования кокса в качестве выгорающей добавки является наличие достаточного количества кислорода в холодной части печи для окисления введенного в шлам топлива. В результате перераспределения топлива, так как часть топлива сжигается с холодного конца печи, с горячего обреза подается топлива меньше на эквивалентную величину замещения. Поэтому топливо в горячей части печи сгорает в условиях повышенного коэффициента избытка воздуха (α), что приводит к снижению температуры факела и, следовательно, снижению теплообмена в зоне спекания. При запредельно высоком α температура продуктов горения может оказаться заниженной настолько, что не обеспечит разогрев материала до температуры спекания клинкера – 1450ºС.
Однако, следует отметить, что температура горения топлива зависит не только от коэффициента избытка воздуха – α, но и от температуры вторичного воздуха, которая определяется эффективностью работы холодильника, то есть зависит от теплопотерь с клинкером – qкл.
Комплекс теплотехнических расчетов был сделан для условий, когда тепловой КПД холодильника изменялся от 0,5 до 1, то есть при изменении qкл от 0 до 800 кДж/кг клинкера. Результаты расчетов температуры факела и удельного теплообмена в зоне спекания в виде номограмм представлены на рис. 3 и свидетельствуют, что достаточно резко эти величины снижаются при вводе в сырьевую смесь более 3% выгорающей добавки и увеличения qкл > 400 кДж/кг клинкера.
Кроме того, как уже говорилось ранее, для использования нефтяного кокса в качестве выгорающей добавки следует также определять необходимую величину удельного теплооб-

Рис. 3. Изменение температуры факела и теплообмена в зоне спекания в зависимости от концентрации выгорающей добавки, теплопотерь с клинкером qкл и коэффициента избытка воздуха α
мена в зоне спекания, достаточную для получения клинкера. Величина теплопередачи от газового потока к материалу должна быть не ниже ≈80кВт/м2, что можно обеспечить при вводе выгорающей добавки в количестве 3,15% (точка А, рис. 4). При этом tф = 1660°С и α = 1,42. Следовательно, максимальная концентрация горючей составляющей в шламе, при которой возможно получить клинкер, может достигать 3%.
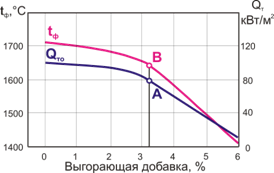
Рис. 4. Изменение температуры факела и теплообмена в зоне спекания в зависимости от концентрации выгорающей добавки
Проблематичным при использовании нефтяного кокса является повышенное содержание в нем SO3 которое может достигать 8%, так как в нашей стране значительную часть в общем выходе составляют сернистые и высокосернистые нефти. Исходя из этого, наиболее эффективным является использование нефтяного кокса в качестве выгорающей добавки на заводах, использующих высокощелочное сырье, что позволяет нейтрализовать негативное воздействие щелочей на процесс обжига клинкера и качество готового продукта. Так как щелочи в первую очередь реагирует с SO3 с образованием устойчивых сульфатов калия и натрия или смешанных щелочно-сульфатных фаз, ввод серы с нефтяным коксом в сырьевую шихту может существенно уменьшить отрицательное влияние щелочей. Повышенное количество SO42- одновременно катализирует процесс связывания CaO и ослабляет тормозящее действие на него ионов Na+ и K+ [2, 6].
Однако при использовании нефтяного кокса в качестве выгорающей добавки возникает опасность возгонки щелочных сульфатов, являющихся летучими компонентами, что существенно усложняет процесс обжига клинкера образованием наростов и кольцеобразованием в зоне цепной завесы в печах мокрого способа и настылей в печах сухого способа производства. Для печей как мокрого, так и сухого способов производства существует возможность решения данной проблемы поддержанием окислительной атмосферы в печи, при которой возгонка щелочных сульфатов минимальна [3]. Так как в печах сухого способа невозможно полностью исключить возгонку, в них необходимо применение байпаса для вывода из системы части щелочесодержащих и сульфатсодержащих отходящих газов. Также обязателен контроль содержащегося в сырьевой смеси количества SO3, возгонка которого оказывает непосредственное влияние на возможность настылеобразования [7].
Таким образом, количество возможно вносимой нефтяным коксом серы для заводов, работающих по мокрому способу производства, будет определяться содержанием щелочей в сырьевой шихте, а для заводов сухого способа – использованием системы байпасирования.
Кроме того, для решения проблемы повышенного содержания серы в коксе существуют технологии по обессериванию нефтяного кокса. Для этого активно используется прокаливание кокса. Еще один путь получения обессеренного нефтяного кокса из высокосернистых марок нефти − это предварительное удаление серы из сырой нефти методом гидрообессеривания, гидрокрекинга или деасфальтизации. Этот вариант считается более действенным, несмотря на то, что является более сложным и требует дополнительных затрат.
Технология применения нефтяного кокса уже апробирована и активно используется на Савинском цементном заводе в Архангельской области. Там применяется нефтяной кокс трех марок калорийностью 7900-8200 ккал/кг с содержанием серы до 4,5%, характеристика которых приведена в табл. 1.
Таблица 1
Характеристика марок нефтяного кокса,
используемого на Савинском цементном заводе
Марка кокса |
Влажность, % |
Летучие, % |
Зольность, % |
Б |
11,41 |
13,83 |
3,53 |
В |
9,73 |
16,93 |
0,44 |
С |
8,26 |
15,11 |
0,52 |
Таким образом, нефтяной кокс благодаря высокой теплотворной способности и низкой зольности является уникальным альтернативным топливом. Максимальное количество его ввода в шлам зависит, в первую очередь, от КПД холодильника и не должно превышать 3-3,5%. Сера, вносимая в сырьевую смесь с коксом, будет связываться с оксидами щелочных металлов и выводиться с клинкером, уменьшая процессы кольцеобразования в холодной части печи в результате снижения циркуляции солей щелочных металлов.
Исследования выполнены при финансовой поддержке РФФИ в рамках научного проекта № НК-14-41-08025/14 р_офи_м.
Рецензенты:Кривобородов Ю.Р., д.т.н., профессор кафедры химической технологии композиционных и вяжущих материалов ГОУ ВПО «Российский химико-технологический университет им. Д.И. Менделеева», г. Москва;
Куликов Б.П., д.х.н., генеральный директор ООО «Безотходные и малоотходные технологии», г. Иркутск.