Несмотря на значительное развитие производства новых синтетических материалов (рулонных, плиточных, листовых, мастичных), древесина для устройства напольных покрытий еще долгое время будет иметь наибольший спрос и распространение, так как она обладает удачным сочетанием положительных свойств. Эти свойства особенно полно обнаруживаются в древесине при ее применении в паркетных полах.
По долговечности, теплоусвояемости и внешнему виду паркетные полы не имеют себе равных. Пол из самого высококачественного линолеума уступает правильно настланному паркету по красоте и комфорту, поэтому паркетные полы служат эффективным средством архитектурного и художественного оформления помещений и создают ощущение комфорта. Благодаря этим качествам паркетные полы широко применяются в общественных и жилых зданиях, украшая любое помещение. К сожалению, паркет из натуральной древесины, будь то дуб или другие ценные породы (ясень, палисандр и т.д.), не может широко применяться из-за ограниченности сырьевых ресурсов и своей высокой стоимости.
Полы должны удовлетворять общим эксплуатационным требованиям: быть долговечными, красивыми и теплыми, обладать звукоизолирующей способностью и в то же время иметь невысокую стоимость [4].
Одним из актуальных направлений научных исследований в деревообрабатывающей отрасли является разработка и внедрение в производство экономически эффективного и технологически приемлемого способа улучшения физико-механических, эстетических и эксплуатационных свойств древесины малоценных лиственных пород для применения в покрытиях пола.
Долговечность пола предопределяется прочностью исходного материала. Основным показателем прочности служит износостойкость, которую определяют способностью сопротивляться разрушению поверхностных слоев в результате трения, возникающего при взаимодействии изделий из древесины с другими твердыми телами или абразивными материалами. Это свойство представляет особый интерес, когда древесина используется в качестве напольных покрытий, ступеней лестниц и т.д. [2]. Ранее величину износа различных пород характеризовали при 1000 шаг/сутки. В настоящее время существует несколько методик испытаний на износостойкость, например, прибором Мартиндейл, который создает фигуры Лиссажу из отличающихся направлением и пространственным расположением царапин. Такой прибор исследовался на возможность применения как для испытаний паркета, так и для испытаний ламината, и больше подходит для исследования износостойкости поверхностного лакокрасочного покрытия полов [5].
В ЦНИИМОД разработан стандартный метод испытаний (ГОСТ 16483.39-81), по которому брусок из древесины истирается в специальном устройстве с помощью шлифовальной бумаги, совершающей возвратно-поступательное и одновременно вращательное движение. Показатель истирания определяется по разнице масс до и после испытаний. Не следует путать этот метод с так называемым Табер-тестом, который предназначен для испытаний износостойкости защитно-декоративных покрытий поверхности древесины и древесных плит [2].
Масштабы пластической деформации, которая имеет место в действительности, зависят от типа износа, которому подвергается покрытие, а также от твердости подложки. Значения ударной твердости и износостойкости некоторых пород древесины приведены в таблице 1.
Таблица 1
Значения ударной твердости и износостойкости некоторых пород древесины
Породы |
Ударная твердость, Дж/см2 |
Показатель истирания поверхности разрезов, мм |
||
поперечного |
радиального |
тангенциального |
||
Лиственница |
0,90 |
0,07 |
0,17 |
0,14 |
Сосна |
0,72 |
0,12 |
0,31 |
0,28 |
Ель |
0,73 |
0,12 |
0,24 |
0,24 |
Акация белая |
1,21 |
0,04 |
0,12 |
0,12 |
Береза |
0,80 |
0,13 |
0,26 |
0,29 |
Бук |
0,96 |
0,06 |
0,14 |
0,12 |
Ясень |
1,07 |
0,05 |
0,14 |
0,15 |
На кафедре механической обработки древесины УГЛТУ ведутся исследования по улучшению физико-механических свойств древесины малоценных лиственных пород модифицированием для применения в покрытиях пола. Образцы радиальной распиловки из древесины осины и березы пропитывались алкидной композицией и после выдержки подвергались прессованию и технологической выдержке.
Полученные образцы испытывались на износостойкость по ГОСТ 21523.10-88 «Древесина модифицированная. Метод определения истирания». Исследования проводились для наиболее популярных, применяемых для напольных покрытий пород древесины, которые были в натуральном виде (вишня, орех, бук, дуб и др.), а также для модифицированной древесины березы и осины.
В ходе проведенных исследований по модифицированию малоценных лиственных пород древесины осины и березы было изучено влияние на физико-механические показатели получаемого материала таких факторов, как время выдержки образцов после нанесения пропиточной композиции до прессования и величина упрессовки.
После нанесения пропиточного состава на поверхность древесины необходима открытая выдержка для более глубокого проникновения состава в древесину и частичного удаления растворителя. От глубины пропитки и степени упрессовки древесины при прессовании зависит плотность, а значит, и прочность модифицированной древесины на истирание.
Испытания проводились при частоте вращения диска испытательной машины 40-1. Каждая пара притертых образцов подвергается истиранию при нагрузке, обеспечиваемой постоянным грузом массой 2600 г и 250 оборотами диска испытательной машины. После испытания образцы вынимаются из машины, очищаются от пыли, взвешиваются, и определяется высота образцов после испытания [1]. Истирание образцов модифицированной древесины по высоте (ih) и по массе (im) в процентах вычисляется по формулам:
где : h1 – высота образца до испытания, мм;
h2 – высота образца после испытания, мм;
m1 – масса образца до испытания, г;
m2 – масса образца после испытания, г.
Полученные результаты и сравнительная характеристика истираемости образцов показана на рис. 1.
Рис. 1. Сравнительная характеристика истираемости образцов различных пород древесины
Дуб является эталонным по физико-механическим показателям материалом для штучного паркета, его истираемость составляет 13 %. Результаты экспериментов показали, что из модифицированной древесины ближе всего к дубу находится берёза, истираемость которой 14 %. Модифицированная осина, истираемость которой 17,5 %, немного уступает по этому показателю и дубу, и клёну, и модифицированной березе, но показывает хорошие результаты в сравнении с необработанной натуральной массивной древесиной осины, у которой истираемость составляет 26 %.
Радиальный паркет лучше сопротивляется износу (истиранию), чем тангенциальный. Истирание его происходит более равномерно, чем истирание тангенциальной планки паркета, в которой годичные слои образуют широкие выходы на пласть мягкой древесины, более подверженной истиранию [3].
Зависимость истираемости осины и берёзы от времени выдержки до прессования и различной упрессовки приведена на рис. 2 и 3.
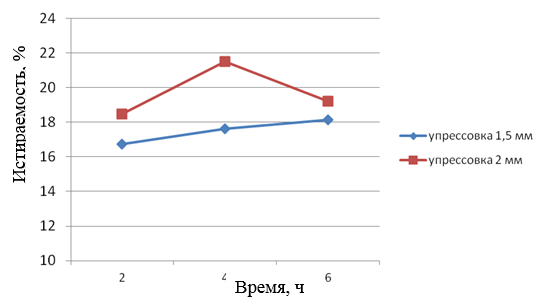
Рис. 2. Зависимость истираемости модифицированной осины от времени выдержки до прессования
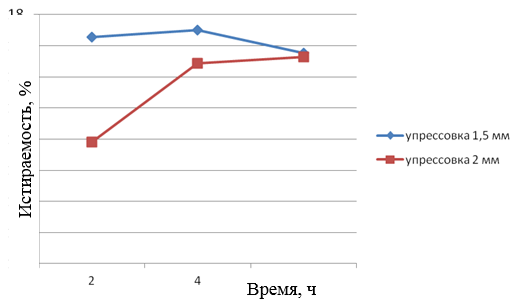
Рис. 3. Зависимость истираемости модифицированной берёзы от времени выдержки до прессования
Древесина осины показывает хорошие результаты при упрессовке 1,5 мм и выдержке до прессования в течение 2 часов. Береза при той же выдержке лучше ведет себя при упрессовке 2 мм. Дальнейшее увеличение времени выдержки древесины после пропитки технологически и экономически нецелесообразно.
В ходе оптимизации процесса модифицирования были установлены оптимальные параметры режима модифицирования, представленные в таблице 2.
Таблица 2
Оптимальные параметры режима модифицирования при пропитке алкидной композицией
Параметры режима модифицирования |
Порода древесины |
|
Осина |
Берёза |
|
Время выдержки до прессования, ч |
2 |
2 |
Упрессовка, мм |
1,5 |
2 |
Температура пропитки, oC |
20 |
20 |
В результате выполненных экспериментально-теоретических исследований получен материал, соответствующий требованиям действующих стандартов и пригодный для использования в качестве паркетных покрытий.
Модифицированная древесина березы и осины по основным физико-механическим показателям имитирует ценные твердолиственные породы древесины и при этом позволяет полностью заменить их в паркетных изделиях. Низкая стоимость исходного сырья уменьшает себестоимость изделий. Данный материал не требует дополнительного нанесения защитно-декоративного покрытия и полностью готов к укладке после механической обработки.
Применение модифицирования малоценных пород древесины позволит расширить сырьевую базу паркетного производства за счет переработки древесины малоценных мягких лиственных пород.
Рецензенты:
Гороховский А.Г., д.т.н., ген. директор ОАО «УралНИИПдрев», г. Екатеринбург.
Уласовец В.Г., д.т.н., профессор кафедры механической обработки древесины ФГБОУ ВПО «Уральский государственный лесотехнический университет», г. Екатеринбург.