Введение
Актуальность эффективного применения импульсных способов сварки, так как данные методы создают наиболее благоприятные условия для активного управления плавлением и переносом электродного металла, тем самым позволяют повысить качество сварки и получить сварной шов с заданными свойствами, представлена в работе [4]. Технологические преимущества импульсно-дуговой сварки позволяют создавать новые более совершенные способы и разрабатывать эффективное сварочное оборудование, имеющее широкие возможности для управления технологическими процессами, а именно процессами плавления и переноса электродного металла и формирования сварного шва.
В статье представлена разработка феноменологической модели управления процессом импульсно-дуговой сварки, основанная на результатах исследований кинограмм процесса импульсно-дуговой сварки в среде углекислого газа в нижнем положении.
Для описания явлений, протекающих в процессе сварки, необходимо разработать модель, которая учитывала бы особенности выбранного способы сварки. Однако разработка модели сварочных процессов – это всего лишь приближения к оригинальному процессу, который стараются идеализировать и упростить для лучшего представления сварочных процессов. Для получения бездефектного сварного соединения сварочная дуга должна обеспечивать:
-
пространственную устойчивость;
-
управляемый перенос электродного металла;
-
требуемые геометрические размеры столба сварочной дуги;
-
необходимые величины силового и теплового воздействия.
Также необходимо установить взаимосвязь между параметрами процесса сварки. Модель управления процессом сварки должна включать в себя входные, внутренние и выходные параметры (рис. 1) [1].
Входные параметры: режим сварки (ток, напряжение, скорость подачи электродной проволоки, диаметр электрода, состав электрода, вылет электрода); защитная среда (активный газ, инертный газ, смесь газов, флюс); способ сварки (механизированная или автоматическая).
Внутренние параметры: силы, действующие на жидкий металл сварочной ванны; световое излучение; тепловое излучение.
Выходные параметры: геометрические размеры сварного шва: ширина, глубина проплавления, высота; геометрические размеры столба сварочной дуги; геометрические размеры сварочной ванны.
Рисунок. 1. Параметры для создания модели управления процессом импульсно-дуговой сварки
Таким образом, установление взаимосвязи между параметрами дает определенные возможности при создании модели для управления процессом импульсно-дуговой сварки.
При сварке в защитных газах на каплю электродного металла действуют следующие основные силы: сила тяжести Fт; сила поверхностного натяжения Fп.н.; электродинамическая сила Fэд; реактивное давление испаряющегося с поверхности капли металла и давления газа Fр; сила давления потоков плазмы и бомбардировки заряженными частицами Fп. [5].
Сила тяжести. Сила Fт оказывает существенное влияние только при больших размерах капель. В зависимости от пространственного расположения шва сила Fт способствует отрыву капли от электрода, если шов расположен в нижнем положении; если шов в потолочном положении, то сила тяжести препятствует отрыву; а если в вертикальном, то сила тяжести отклоняет каплю от электрода.
Сила поверхностного натяжения. Сила Fп.н. обычно препятствует переносу капель с электрода в ванну. Местом приложения силы Fп.н. может быть принято такое сечение на жидкой капле, в котором эта сила минимальна.
Электродинамическая сила. Сила Fэд возникает при прохождении тока по проводнику из-за взаимодействия тока с собственным магнитным полем. Если сечение проводника постоянно, то эта сила направлена по радиусу к оси проводника и стремится его сжать.
Реактивная сила Fр. Расплавленный металл на электроде и изделии в зоне активных пятен находится при температуре, близкой к температуре кипения. По этой причине с поверхности активных пятен происходит интенсивное испарение, а иногда и выделение различных газов. Из газов, которые могут образовываться на электроде, существенно образование окиси углерода.
Объемное действие сил и графическое отображение сил на ось электрода при сварке в нижнем положении представлено в таблице 1.
Таблица 1 – Силы, действующие на каплю электродного металла
Силы |
Fт |
Fп.н. |
Fр. |
Fэд |
FΣ |
Объемное действие сил |
|
|
|
|
|
Графическое отображение сил |
|
|
|
|
|
Рассмотреть в чем заключается сущность активного управления плавлением и переносом электродного металла возможно при исследовании процесса импульсно-дуговой сварки с помощью скоростной киносъемки, методика которой описана в работах [2, 3].
Полный цикл процесса плавления и переноса электродного металла при импульсно-дуговой сварке в углекислом газе в нижнем положении представлен на рисунке 2.
Рис. 2. Кинограммы процесса плавления и переноса электродного металла при импульсно-дуговой сварке в углекислом газе в нижнем положении (скорость съемки 2980 кадр/сек)
На основе анализа кинограмм процесса плавления и переноса электродного металла при импульсно-дуговой сварке в углекислом газе в нижнем положении разработана схема цикла данного процесса (рис. 3).
Рис. 3. Схема цикла процесса импульсно-дуговой сварки в углекислом газе
Этап паузы можно описать следующим образом (рис. 4).
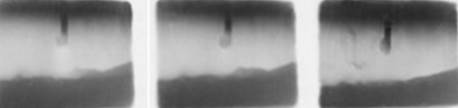
1 2 3
4 5 6
7 8 9
Рис. 4. Кинограммы процесса плавления и переноса электродного металла при импульсно-дуговой сварке в углекислом газе в нижнем положении на этапе паузы (скорость съемки 2980 кадр/сек)
На кадре 1 показан небольшой столб дуги. На торце электрода находится капля. Под действием давления дуги капля вытесняется на его боковую поверхность. На кадрах 2-8 столб сварочной дуги практически не виден. На кадрах 3-4 видно, как капля начинает приподниматься относительно торца электрода. Электрод со стороны капли оплавляется косо. На кадре 5 капля электродного металла начинает выравниваться. На кадрах 6-8 наблюдается рост и смещение капли относительно оси электрода. На кадре 9 видно увеличение столба сварочной дуги. Под действием силы тяжести и поверхностного натяжения капля сформировалась на торце в виде сферы. Капля электродного металла занимает соосное положение с электродом.
Действие сил на каплю и результирующее действие сил при импульсно-дуговой сварке в нижнем положении показано на рисунке 5. Как видно, на этапе паузы сила тяжести направлена вниз, а все остальные силы, а именно сила поверхностного натяжения, реактивная сила и электродинамическая сила, направлены вверх. Результирующая составляющая действия всех сил на каплю электродного металла будет равна нулю, т.е. капля находится в равновесном состоянии.
Рис. 5. Действие сил и результирующее действие сил при импульсно-дуговой сварке в нижнем положении на этапе паузы
Этап нарастания тока импульса можно описать следующим образом (рис. 6). На кадре 1 (появилась) показана небольшая дуга. На торце электрода хорошо видна капля. Занимает соосное положение с электродом. Диаметр столба меньше диаметра капли и электрода. На кадре 2 наблюдается увеличение столба сварочной дуги. За счет увеличения тока импульса и величины сил, действующих на каплю. На кадре 3 столб увеличился, принимает бочкообразную форму и постепенно обхватывает каплю электродного металла. Нарастание тока происходит плавно, капля втягивается в столб дуги и, не смещаясь на боковую поверхность электрода, занимает соосное с ним положение.
1 2 3
Рис. 6. Кинограммы процесса плавления и переноса электродного металла при импульсно-дуговой сварке в углекислом газе в нижнем положении на этапе нарастания тока импульса (скорость съемки 2980 кадр/сек)
Действие сил на каплю и результирующее действие сил при импульсно-дуговой сварке в нижнем положении показано на рисунке 7. Как видно, на этапе нарастания тока импульса сила тяжести и электродинамическая сила направлены вниз, а сила поверхностного натяжения и реактивная сила направлены вверх. В этом случае результирующая составляющая действия всех сил на каплю электродного металла будет стремиться оторвать каплю электродного металла в сторону сварочной ванны.
Рис. 7. Действие сил и результирующее действие сил при импульсно-дуговой сварке в нижнем положении на этапе нарастания тока импульса
Этап отрыва капли электродного металла можно описать следующим образом (рис. 8). На кадре 1 столб дуги обхватывает каплю электродного металла. С нарастанием сварочного тока увеличивается и значение электродинамической силы, под действием которой капля втягивается в столб дуги и движется в сторону ванны. На кадре 2 видно образование шейки между электродом и каплей. Происходит оттягивание капли в направлении ванны. На кадре 3 происходит отрыв капли и ее ускорение в сторону сварочной ванны. Показана оторвавшаяся капля. После разрыва перемычки реактивное давление паров очень большое, поэтому капля сильно деформирована. При взрыве шейки и отрыве капли, дуга «прыгает» на электрод, обхватывая его, поэтому в этот момент диаметр столба имеет наибольшие размеры.
1 2 3
Рис. 8. Кинограммы процесса плавления и переноса электродного металла при импульсно-дуговой сварке в углекислом газе в нижнем положении на этапе отрыва капли электродного металла (скорость съемки 2980 кадр/сек)
Действие сил на каплю и результирующее действие сил при импульсно-дуговой сварке в нижнем положении показано на рисунке 9. На этапе отрыва капли электродного металла все силы направлены вниз, кроме реактивной силы, которая в данный момент отсутствует. Сила тяжести, сила поверхностного натяжения и электродинамическая сила направлены вниз, причем значение электродинамической силы очень большое. В этом случае очевидно значение результирующей составляющей действия всех сил на каплю электродного металла, которая направляет каплю электродного металла в сварочную ванну.
Рис. 9. Действие сил и результирующее действие сил при импульсно-дуговой сварке в нижнем положении на этапе отрыва капли электродного металла
Этап перехода капли электродного металла в сварочную ванну можно описать следующим образом (рис. 10). На кадре 1-3 показана сильно деформированная капля, парящая в направлении сварочной ванны. Ток уменьшается. Наблюдается сужение столба сварочной дуги.
1 2 3
Рис. 10. Кинограммы процесса плавления и переноса электродного металла при импульсно-дуговой сварке в углекислом газе в нижнем положении на этапе перехода капли электродного металла в сварочную ванну (скорость съемки 2980 кадр/сек)
Действие сил на каплю и результирующее действие сил при импульсно-дуговой сварке в нижнем положении показано на рис. 11. На этапе перехода капли электродного металла в сварочную ванну сила тяжести, сила поверхностного натяжения и электродинамическая сила направлены вниз. В том же направлении действует результирующая составляющая действия всех сил на каплю электродного металла. Как видно, капля электродного металла входит в сварочную ванну.
Рис. 11. Действие сил и результирующее действие сил при импульсно-дуговой сварке в нижнем положении на этапе перехода капли электродного металла в сварочную ванну
Этап спада тока импульса можно описать следующим образом (рис. 12).
1 2 3
Рис. 12. Кинограммы процесса плавления и переноса электродного металла при импульсно-дуговой сварке в углекислом газе в нижнем положении на этапе спада тока импульса (скорость съемки 2980 кадр/сек)
На кадрах 1-3 видим постепенно уменьшающийся столб сварочной дуги. Капля металла перешла в сварочную ванну. На торце электрода видна вновь образованная капля расплавленного металла (кадры 1-3).
Феноменологическая модель управления процесса импульсно-дуговой сварки в среде углекислого газа в нижнем положении представлена на рисунке 13. За основу на каждом этапе взята результирующая составляющая действия сил на каплю электродного металла.
Рис. 13. Феноменологическая модель управления процесса импульсно-дуговой сварки в среде углекислого газа в нижнем положении
Таким образом, на основе анализа кинограмм процесса импульсно-дуговой сварки в среде углекислого газа в нижнем положении разработана феноменологическая модель процесса импульсно-дуговой сварки.
Выводы
-
На основе анализа кинограмм процесса плавления и переноса электродного металла при импульсно-дуговой сварке в углекислом газе в нижнем положении предложена схема цикла данного процесса, который разбит на этапы: этап паузы и этап импульса.
-
Разработана феноменологическая модель, которая учитывает особенности выбранного способа сварки с учетом получения бездефектного сварного соединения.
Рецензенты:
Петрушин С.И., д.т.н., профессор кафедры Технологии машиностроения Юргинского технологического института Томского политехнического университета, г. Юрга.
Сапожков С.Б., д.т.н., профессор кафедры Сварочного производства Юргинского технологического института Томского политехнического университета, г. Юрга.