В последнее время сварка трением с перемешиванием все чаще применяется для изготовления ответственных изделий, в том числе, цистерн для перевозки различных жидкостей и газов, сосудов, работающих под давлением, а также корпусных деталей ракетно-космической техники. Поэтому, развитию неразрушающих методов контроля для диагностики сварных швов, полученных данным методом, уделяется особое внимание.
Существует два метода неразрушающего контроля, которые позволяют обнаруживать дефекты в объеме сварного шва – радиография и ультразвуковая дефектоскопия, однако метод радиографии напрямую не позволяет определять глубину расположения дефекта. Это возможно сделать только с использованием дорогостоящих рентгеновских томографов, которые, кроме того, имеют существенные ограничения по размеру контролируемого образца, что делает невозможным их применение для контроля изделий крупного размера в промышленном производстве.
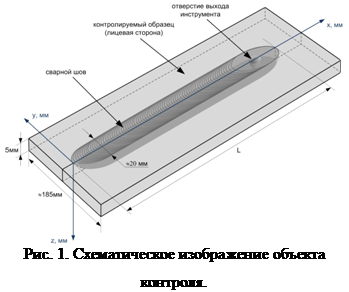
Целью данной работы являлась разработка методики обнаружения дефектов при ультразвуковом сканировании методом ФАР в сварных соединениях из алюминиевого сплава АМг5, полученных методом СТП.
Методика контроля
Образец для отработки методики контроля был получен сваркой трением перемешиванием из листов термически неупрочняемого деформируемого сплава АМг5М в отожженном состоянии (рис. 1). Сварка проводилась на опытно-промышленной установке ЗАО «Чебоксарское предприятие «Сеспель» [1].
Cваривались пластины толщиной 5 мм, ширина образца после сварки составляла »185 мм, ширина сварного шва »19 мм, длина сварного соединения »500 мм.
Ультразвуковой (УЗ) контроль осуществлялся с использованием дефектоскопа с фазированной антенной решеткой «HARFANG VEO 16:128» производства «Sonatest». Для ввода УЗ-луча в образец использовалась угловая призма X3-SB57-N55S производства «Sonatest» с углом ввода 360. В качестве пьезоэлектрического преобразователя (ПЭП) использовался 1D 64-х элементный ультразвуковой датчик ФАР X3-PE-10M64E0.6P производства «Sonatest» с частотой 10Мгц. Элементы в данном ПЭП расположены по одной линии. Одновременно для формирования УЗ-луча может использоваться 16 элементов.
Проведенные ранее исследования сварных соединений, полученных методом СТП, показали наличие специфических дефектов, присущих только данному виду сварки [4-6]. Кроме того, было обнаружено, что скрытые дефекты при СТП, как правило, имеют значительно меньший размер по сравнению с дефектами, характерными для сварки плавлением. Поэтому, для проведения контроля был выбран ПЭП с частотой 10 МГц. Такая частота, с одной стороны, обеспечивает достаточную глубину прозвучивания, с другой стороны, позволяет выявлять дефекты минимального размера.
Так как лицевая сторона сварного соединения обладает выраженным чешуйчатым рельефом, а на корневой стороне возможно выдавливание зоны ядра, установка призмы непосредственно на шов с любой из его сторон не представляется возможной. Таким образом, для СТП швов, без дополнительной подготовки поверхности, невозможно использовать прямые призмы. Поэтому, для ввода ультразвукового луча в образец использовалась наклонная призма с углом наклона 360.
Особенностью сварных соединений, полученных методом СТП, также является большое соотношение ширины лицевой стороны шва по отношению к толщине свариваемых пластин. В частности, в данной работе исследовались образцы толщиной 5мм при ширине лицевой стороны шва 19мм. Из-за такой ширины шва не представлялось возможным установить призму ближе 9,5мм от осевой линии шва. Кроме того, из-за возможности наличия грата вдоль краев шва на лицевой стороне, необходимо отодвинуть призму еще на 1-2мм от края шва. В то же время, увеличение расстояния до шва увеличивает путь УЗ-луча до возможных дефектов, соответственно, уменьшает интенсивность отражений от них и вероятность их обнаружения. С учетом вышесказанного, призма устанавливалась так, чтобы расстояние от её переднего края до осевой линии шва составляло 11мм, и соответственно до края шва – 1.5мм.
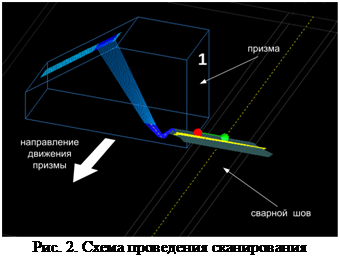
Секторные сканы (S-сканы) поперечного сечения шва записывались с одинаковым пространственным шагом по сигналам датчика пути, и строилась полная УЗ-дефектограмма сварного соединения. При записи дефектограмм, для достижения максимального пространственного разрешения вдоль линии сварного соединения использовался минимальный возможный шаг, который обеспечивал поставляемый в комплекте с дефектоскопом датчик пути – 0.2мм.
В методе ФАР для построения секторного скана, особенно при больших углах сектора сканирования и высоком угловом разрешении, необходимо проведение большого количества вычислительных операций в реальном времени, что ограничивает количество сканов, которые можно получить в единицу времени. Поэтому скорость перемещения призмы вдоль шва ограничена быстродействием вычислительной системы дефектоскопа. Она должна выбираться максимально большой, но, при этом, обеспечивающей запись секторных сканов с необходимым пространственным разрешением без пропусков. В данном случае такая скорость составляла около 2мм/с.
Для обеспечения ввода акустического луча в образец необходимо, с одной стороны, обеспечить минимальное расстояние между призмой и образцом, и с другой стороны, обеспечить присутствие между ними тонкой пленки иммерсионной жидкости. При недостаточном усилии прижима ухудшение акустического контакта может приводить к потерям сигнала на интерфейсе призма-образец. Избыточное усилие может привести к частичному или полному выдавливанию иммерсионной жидкости из зазора и к ухудшению либо потере акустического контакта.

Как было отмечено выше, особенностью СТП-сварных соединений является большое соотношение ширины шва и толщины свариваемых пластин. Это требует тщательного подбора угловых параметров ввода УЗ-луча в образец. Программное обеспечение дефектоскопа существенно облегчает эту задачу за счет наглядной визуализации процесса и отображения изменения параметров в реальном времени, в том числе в процессе сканирования. На рис. 2 приведена графическая схема получения секторного скана. Перед выбором параметров ввода луча в образец необходимо задать геометрические параметры сварного соединения для корректного отображения маски шва. Отображение положения призмы, маски сварного шва в нескольких отражениях, линии фокусировки и области сканирования позволяет подобрать линейку из 16 излучающих элементов ФАР, начальный и конечный угол ввода (aн и aк. на рис. 3) Согласно руководству по эксплуатации дефектоскопа, при углах ввода более 300, которые требуются в данном случае, для сканирования нужно использовать поперечную волну.
Начальный, конечный углы ввода, линейка излучающих элементов, положение и длина области сканирования в направлении распространения луча подбираются совместно, таким образом, чтобы в область сканирования попало всё поперечное сечение сварного шва хотя бы в одном отражении. При этом, нужно придерживаться следующих правил.
Сочетание параметров сканирования должно обеспечивать минимально возможное расстояние до контролируемой зоны с минимальным количеством отражений. Для этого стараются выбирать линейку из 16 излучающих элементов расположенных как можно ближе к переднему краю призмы. При этом, должно отсутствовать пересечение УЗ-луча с передней поверхностью призмы.
Необходимо добиваться минимального значения конечного угла ввода, так как при его увеличении усиливается затухание поперечной звуковой волны, а при больших конечных углах – переход части её энергии в энергию поверхностной волны.
Руководствуясь данными принципами для контроля СТП швов были подобраны следующие значения параметров. Для формирования УЗ-луча использовались элементы с 46 по 61. Начальный и конечный углы ввода составляли aн = 450 и aк = 650. При этом удалось добиться попадания маски шва целиком в область сканирования в 3 и 4 отражениях. Для обнаружения дефектов в сварном соединении, по нашему мнению, наиболее подходит вид фокусировки по постоянной глубине. В данном случае выбранное фокусное расстояние обеспечивало линию фокусировки примерно по середине высоты образца (толщины пластины) в третьем отражении (рис. 3).
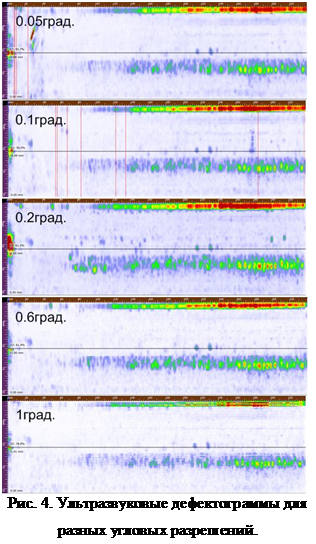
Анализ дефектограмм показывает, что обнаруженный дефект в виде горизонтальной полосы примерно посередине представляет собой цепочку несплошностей тянущихся вдоль сварного шва на расстоянии 3-5мм от его осевой линии по наступающей стороне. В англоязычной литературе дефект такого типа носит название «wormhole»
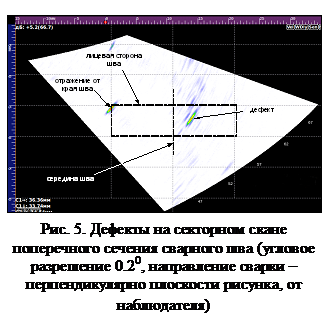
Определить глубину залегания дефектов можно рассмотрев сечение дефектограммы, которое представляет собой скан поперечного сечения шва с использованием специального программного обеспечения, входящего в комплект поставки дефектоскопа. На рис. 5 такое сечение приведено в качестве примера. При корректном задании маски шва применение метода ФАР позволяет точно определить пространственное положение дефекта в сечении сварного соединения непосредственно по шкале дефектоскопа. В данном случае видно, что дефект типа «wormhole» находится на расстоянии 4мм от середины шва на глубине 2–2.5мм от поверхности на набегающей стороне шва. Еще один дефект – отражение от края шва, находится на лицевой стороне на краю шва с отступающей стороны.
Заключение
Проведенные в работе исследования показывают, что представленная методика, разработанная для ультразвуковой диагностики сварных соединений с использованием ФАР, полученных методом СТП является вполне работоспособной и может применяться для контроля швов. Это подтверждают данные дефектоскопии участка сварного соединения, которые свидетельствуют о хорошей выявляемости дефектов, повторяемости и достоверности полученных результатов.
Работа выполнена по проекту № III.23.2.4 фундаментальных исследований СО РАН на 2013–2016 гг., при финансовой поддержке Министерства образования и науки РФ (договор № 02.G25.31.0063) в рамках реализации Постановления Правительства РФ №218.
Рецензенты:Колубаев А.В., д.ф.-м.н., профессор, заведующий лабораторией физики упрочнения поверхности Институт физики прочности и материаловедения СО РАН, г. Томск;
Сизова О.В., д.т.н., главный научный сотрудник Институт физики прочности и материаловедения СО РАН, г. Томск.
Библиографическая ссылка
Рубцов В.Е., Рубцов В.Е., Колубаев Е.А., Колубаев Е.А., Тарасов С.Ю., Тарасов С.Ю. МЕТОДИКА УЛЬТРАЗВУКОВОГО КОНТРОЛЯ СВАРНЫХ СОЕДИНЕНИЙ, ПОЛУЧЕННЫХ СВАРКОЙ ТРЕНИЕМ С ПЕРЕМЕШИВАНИЕМ, С ИСПОЛЬЗОВАНИЕМ ТЕХНОЛОГИИ ФАЗИРОВАННОЙ АНТЕННОЙ РЕШЕТКИ // Современные проблемы науки и образования. 2014. № 6. ;URL: https://science-education.ru/ru/article/view?id=16485 (дата обращения: 02.08.2025).